Industrial Robot Trends In 2024
Top 5 Industrial Robot Trends In 2024
Robots are becoming more sophisticated and skilled as robotic technology advances at an extraordinary rate. From industrial manufacturing to food and beverage and pharmaceutical, robots are being used in numerous industries to automate what were once manual tasks by improving inefficient production lines and enhancing overall productivity. With the year 2024 upon us, it's worth looking at the top five industrial robot trends that we can expect to see in the coming year.
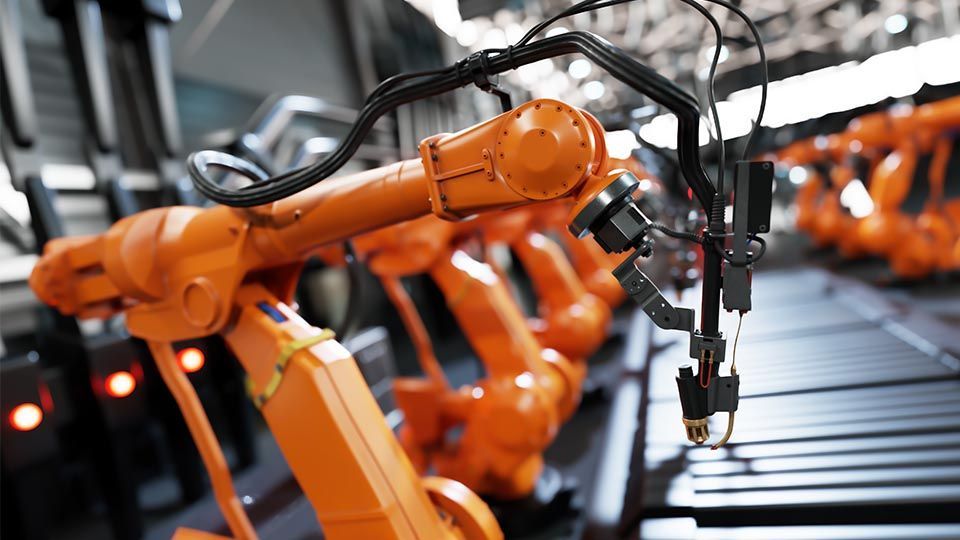
These industrial robot trends include advancements in machine learning, the integration of cobots into our daily lives, the development of more affordable robot services, and the continued expansion of the global industrial robotics market. Let's explore these exciting developments a bit more as I break them down in more detail below.
The top 5 trends in industrial robotics for 2024.
Below, I list what I consider the top five trends in industrial robotics for 2024.
#5 Cobots
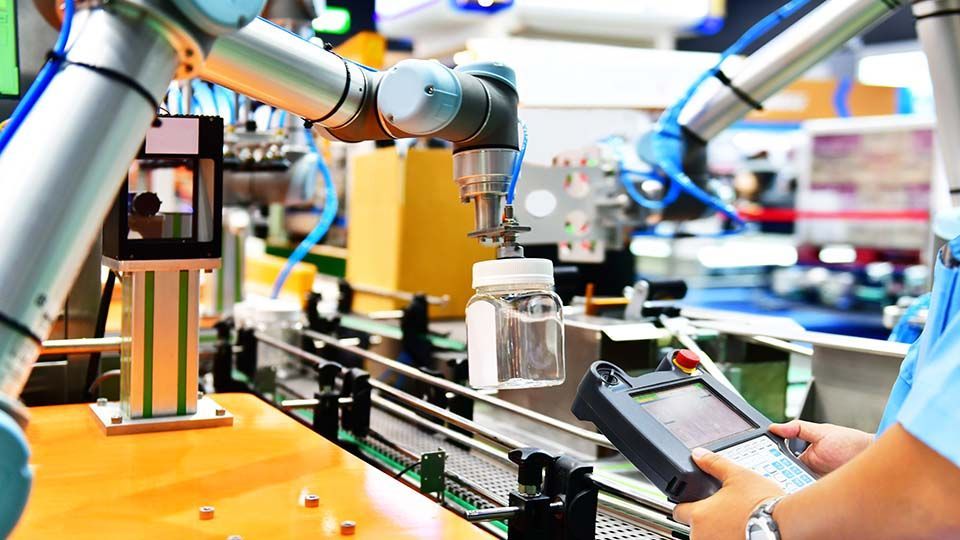
Collaborative Robots, also known as cobots, have become a significant part of the industrial automation industry over the last several years, and we will continue to see that trend grow in 2024.
A cobot is extremely versatile since it can work in conjunction with humans in production because of various safety features. Cobots are very useful with tasks such as:
- Packaging
- Palletizing
- MIG Welding
- Polishing
- Machine Tending
- CNC
- Stamping
- Injection Molding
- Visual Inspection
What are the benefits of collaborative robots?
Below, I list the many benefits of using a collaborative robot.
- Low-Volume Flexibility: The most significant advantage of using a cobot over a standard industrial robot is its flexibility with low-volume production of multiple product variations. Robot programming time is very fast, giving the robot programmer less required setup time during a part changeover or with product variations.
- Floor Space: Cobots can easily be moved and take up much less of a footprint and floor space than the more traditional and larger industrial robots.
- Easy User Interface: The user interface experience is often much simpler and easier to learn than programming an industrial robot. This means the barrier to entry for programmers is significantly lowered while at the same time the deployment and return on investment (ROI) of the robot is quicker.
- Collaborative With Humans: Cobots are small enough that they can share the same workspace with an assembly line worker to complete tasks together. Most collaborative robots have safety features that include extremely sensitive collision sensors, so if something touches the robot, it will stop the motion to avoid a crash with a human or object.
- Energy Efficient: Cobots are more eco-friendly than industrial robots. Companies are looking to reduce electrical costs to help them become more sustainable in their manufacturing process using cobots.
- Cost Effective: Small companies that need to be cost-conscious and have lower budgets can now look to cobots to help with production due to manufacturing labor shortages.
#4 Robots-as-a-Service (RaaS)
Robots-as-a-Services (RaaS) allow companies to leverage automation equipment and related automation software on a subscription or pay-as-you-go basis. This service allows companies to pick and choose the automation equipment they need when they need it. Companies can now replace or upgrade automation and robotic equipment without highly expensive setup costs traditionally seen with automation infrastructure, lowering the barrier for companies to enter the space.
What is the benefit of robots-as-a-service (RaaS)?
Below, I list the many advantages of using RaaS.
- Lower Cost: Companies implementing RaaS have far less upfront equipment costs, leading to a faster ROI than costly-owned equipment.
- Increased Flexibility: RaaS solutions are great for companies with increased flexibility in their automation implementations. The installation process is much easier. Therefore, it is faster than the traditional installation of automation equipment. It is also much easier to increase volume to meet production demand or change and remove programs depending on production needs. RaaS customers do not have to worry about an owned solution that could become obsolete in a year or two because they can easily upgrade their automation systems to the latest and greatest.
- Access To Experts: One of the best aspects of RaaS for automation is the continued support and guidance from the automation provider. Having a direct line to the automation experts for troubleshooting production, experienced integration teams, or finding new automation technology, the service provider can help their customers.
#3 Autonomous Mobile Robots (AMRs)
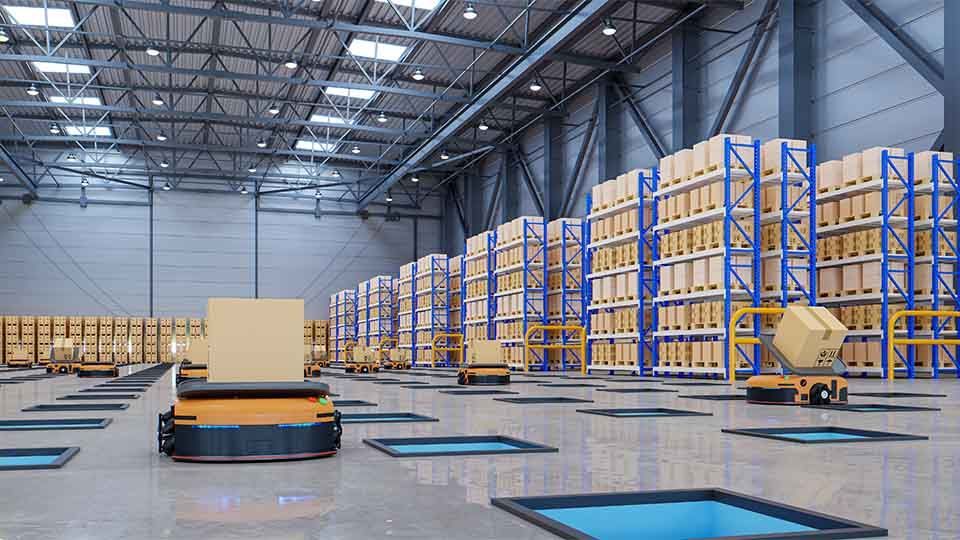
Autonomous Mobile Robots (AMR) and Automated Guided Vehicles (AVG) will continue with their growth momentum. Experts believe that the mobile robot market forecasts will grow tremendously as we move towards 2030, especially in smart factory warehouses and logistics companies as they look to innovate their operational efficiency. This is why many companies are turning to autonomous mobile robots for help.
AMRs are untethered robots that use highly sophisticated sensors, machine learning, and artificial intelligence (AI), and they can calculate for path planning to interpret and navigate through their environment. AMRs can move around objects, avoid collisions, stop, and even reroute themselves because they are equipped with cameras and sensors to help them navigate their environment to complete their task.
What is the difference between AMRs and AGVs?
It is important to know the difference between AMR and AVG robots. Below, I list the definitions.
Autonomous Mobile Robots (AMRs): This type of robot that understands and moves around its environment independently.
Autonomous Guided Vehicles (AGVs): This type of robot relies on predefined paths or tracks to follow and often will require some operator oversight.
Why use an autonomous mobile robot?
Below, I list the many advantages of using AMRs.
- Increase Flexibility: These robots are designed to interact with their environment while completing a variety of programmed tasks, making them unique robots that can be used with many applications and industries.
- Increased Safety: Many companies use AMRs for tasks that would be considered too dangerous for humans to transport or move.
- Increase Efficiency: Companies use AMRs to assist with locating, picking, or moving objects. This allows employees to focus on higher-value work activities.
#2 Machine Learning
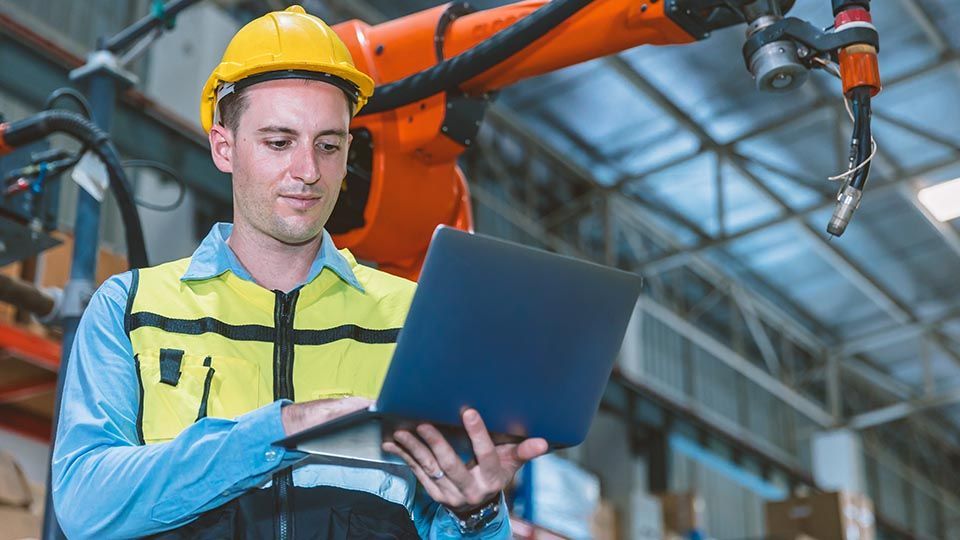
I expect to see a continued increase in industrial robots using machine learning and artificial intelligence (AI) to improve robotic processes. I believe that one of the most significant areas of improvement will be the capabilities of an industrial robot to adapt and learn. Over the past several years, we have seen significant advances in machine learning algorithms. Now, industrial robots can process and analyze enormous amounts of data so quickly that they can make real-time decisions to improve performance.
We will also start seeing more industrial robots notify their users of scheduled maintenance and identify preventative maintenance before failure. A robot that can use these machine learning algorithms to plan its own preventative maintenance schedule has a massive potential to decrease downtime for its user.
#1 Refurbished Robots
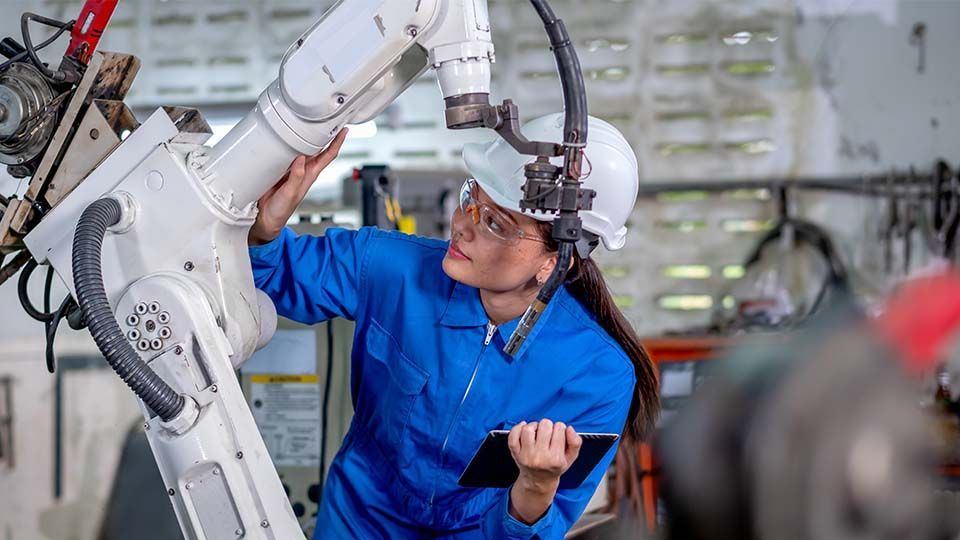
Refurbished or used industrial robots are becoming increasingly common as companies try to find the most cost-effective solutions to implement robotic process automation in manufacturing. Buying refurbished robots allows companies to visit the robots before purchasing or installation. Refurbished robots are freshly greased and have new paint, and worn-out parts are replaced with new ones. Used industrial robot companies to put the robot through vigorous cycle testing of the entire system to ensure it will operate correctly.
What are the benefits of purchasing refurbished industrial robots?
Below, I list a few key benefits of why companies buy refurbished industrial robots.
- Decreased Lead Times: Many robot manufacturers have lead times that are greater than six or nine months for purchasing new robots. It is likely that you can find the used robots that you are looking for and have them shipped to your facility within a month.
- Robot Variety: Companies that sell used industrial robots often have a variety of choices a customer can choose from. So, no matter what make or model you might be looking for, the supplier or a supplier is likely to have that robot model in stock.
- Cost Savings: The cost savings can be massive depending on the number of robots purchased, as used robots can be cheaper by 50% or more.
Industrial Robot Trends in 2024
In conclusion, 2024 is another promising year for the robotics and manufacturing industry because of the continued advancements within the industrial sector. The use of machine learning with AI to predict downtime, the collaborations between robots and humans, and the increasing popularity of using refurbished industrial robots are just a few of the critical robotics trends shaping the future of the industrial robotics industry.
Additionally, with an increased focus on cost efficiency, the increase of robots as a service is more beneficial to many startup companies. We are also seeing a major uptick in mobile robots being used in warehouse factories to help with material transportation.
I expect industrial robots to become even more adaptable, energy-efficient, and cost-effective than ever before in 2024. As the industrial robotics market progresses, it will undoubtedly revolutionize various industrial sectors, making them more efficient, productive, and safer. These technological advancements in robotics and their programming tools have made it easier for programmers to create and modify robotic programs, reducing the time and resources required to implement and maintain robotic systems. This trend will continue for many more years to come.
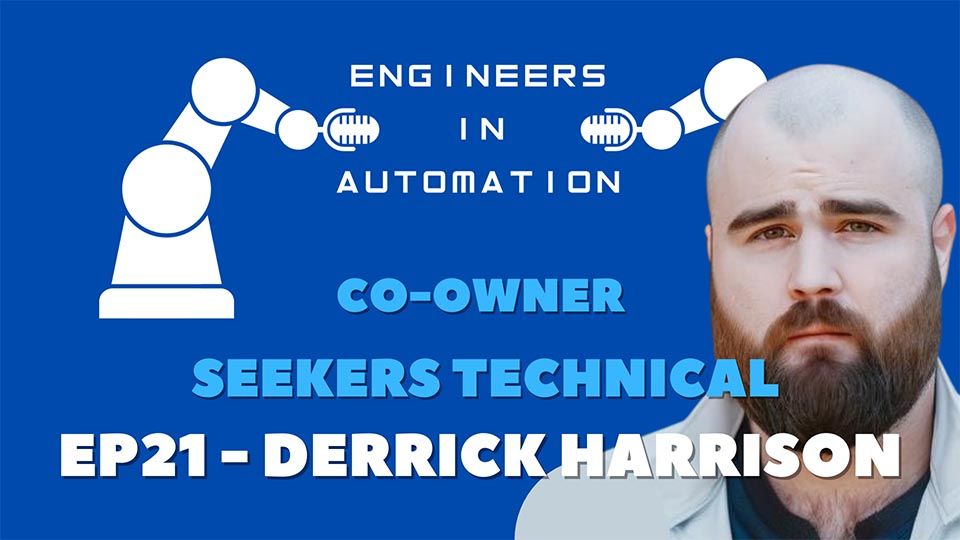
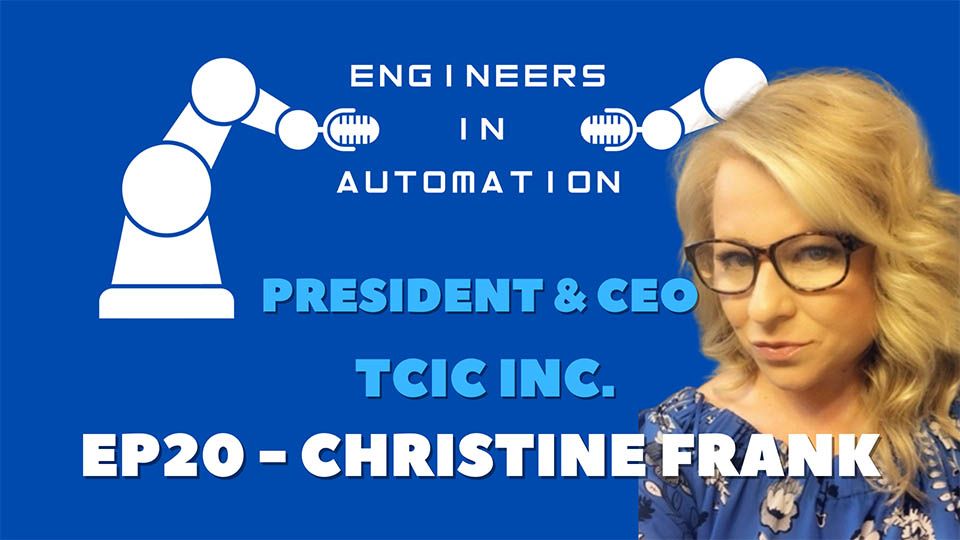
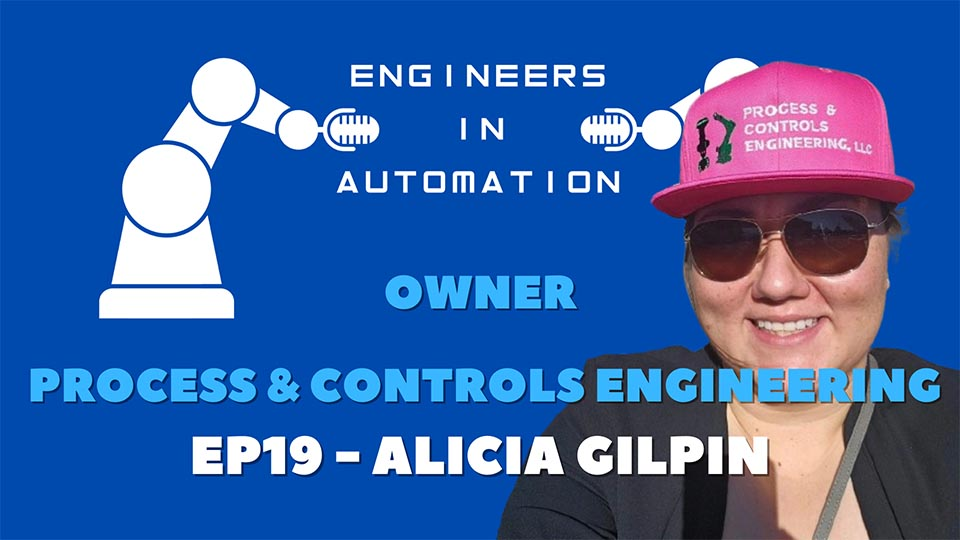
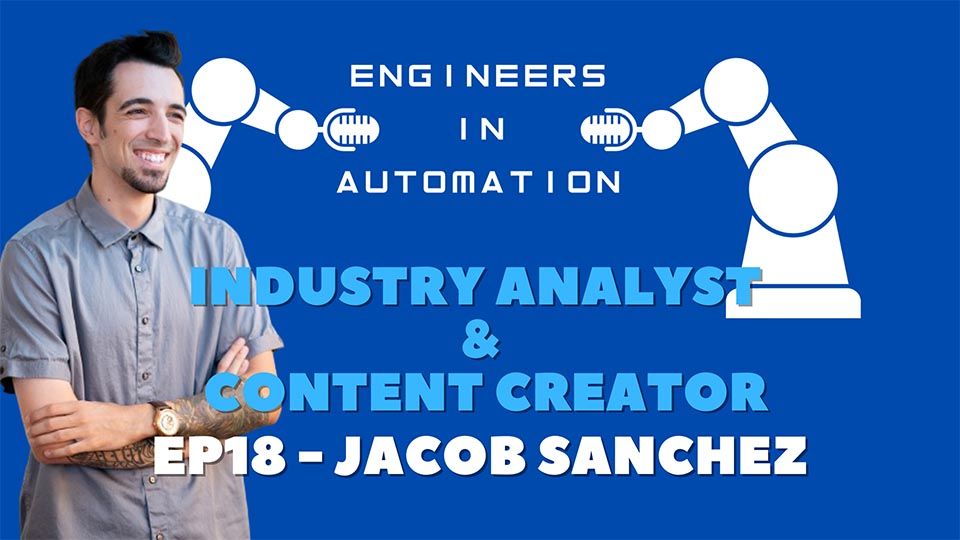
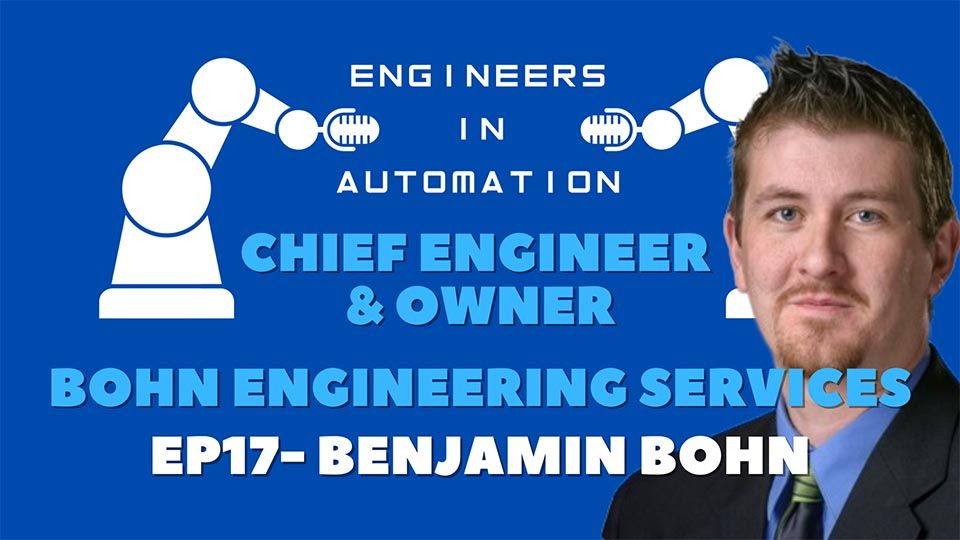
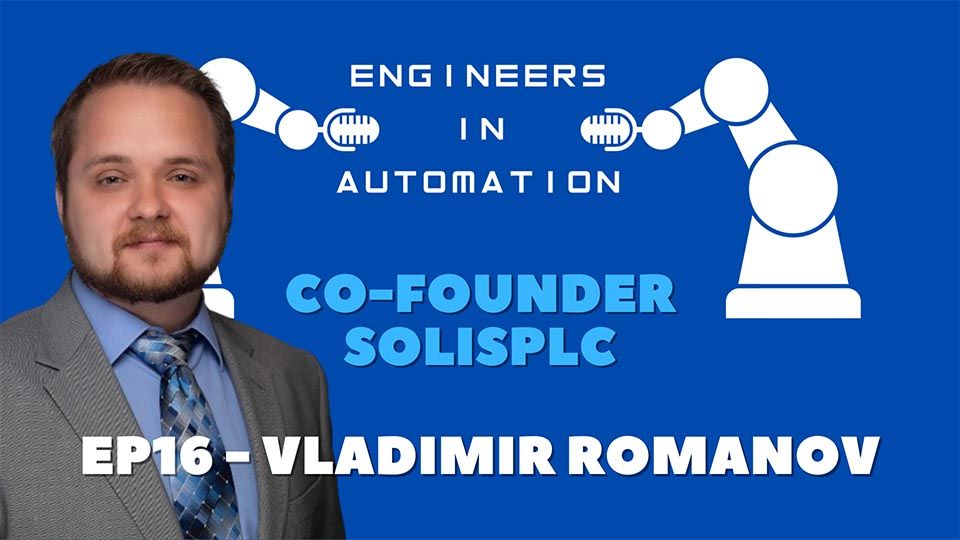
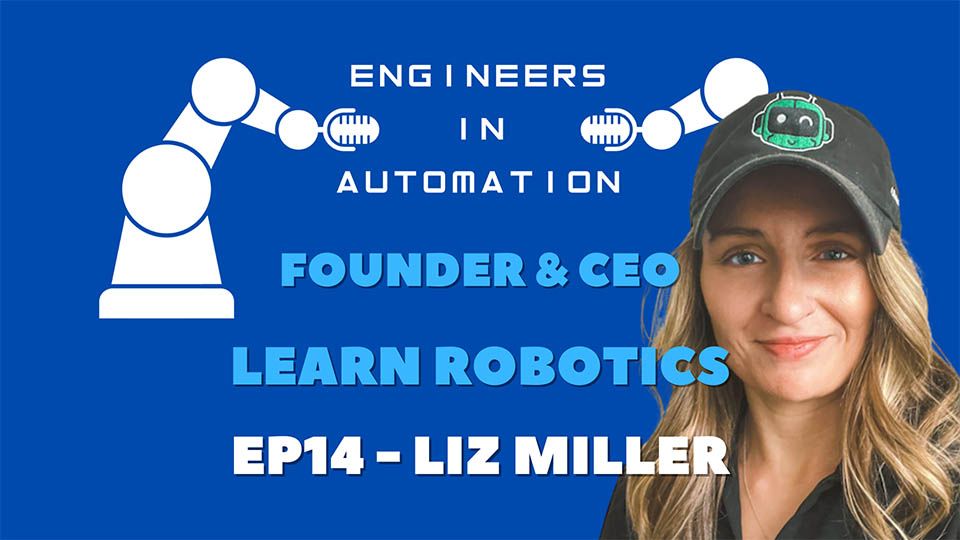
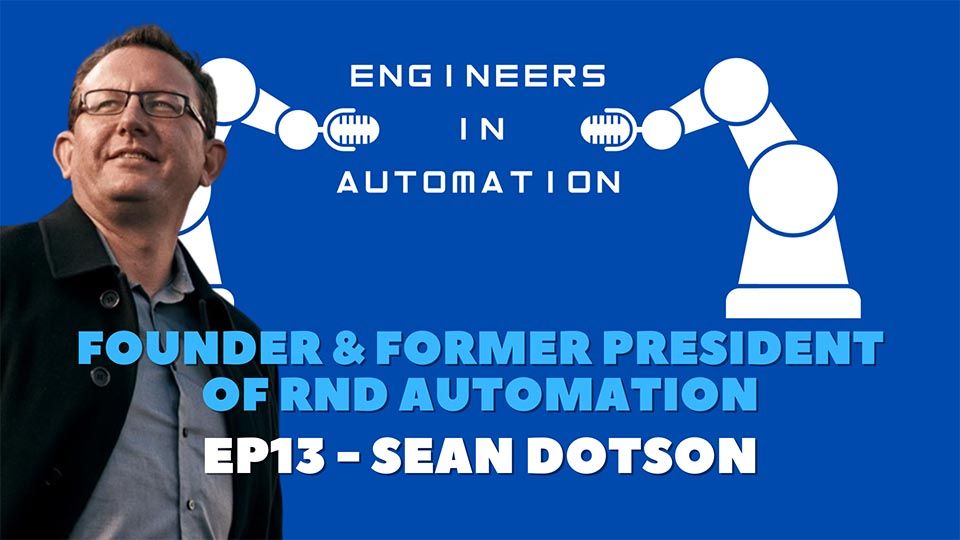
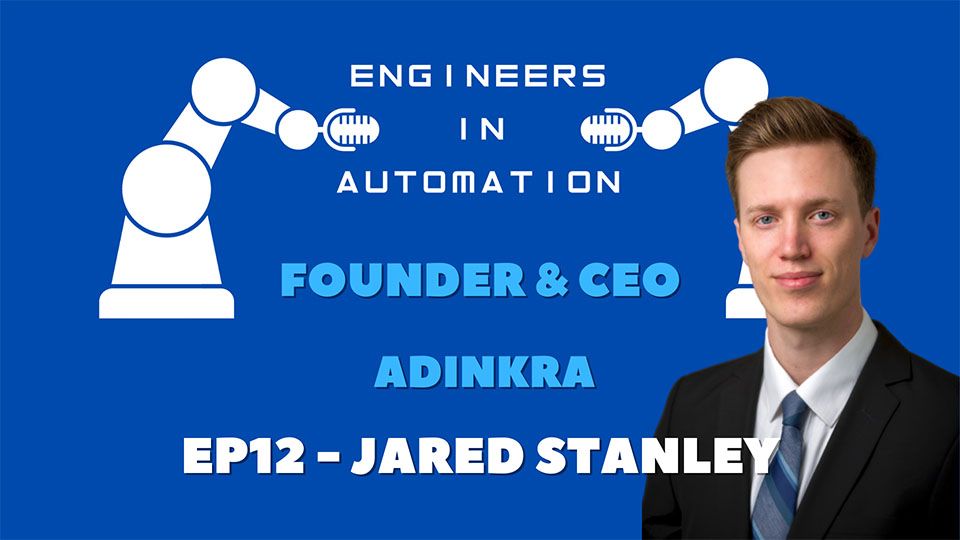